A down payment is often one of the most challenging barriers for people to purchase a home. Making a 20% down payment is difficult for many individuals, therefore they believe they will not be able to buy a house. There are actually ways to buy a house with no down payment. You can utilize many different strategies to make your dream of homeownership a reality.
Stamped Concrete vs. Pavers: The Ultimate Homeowner’s Guide
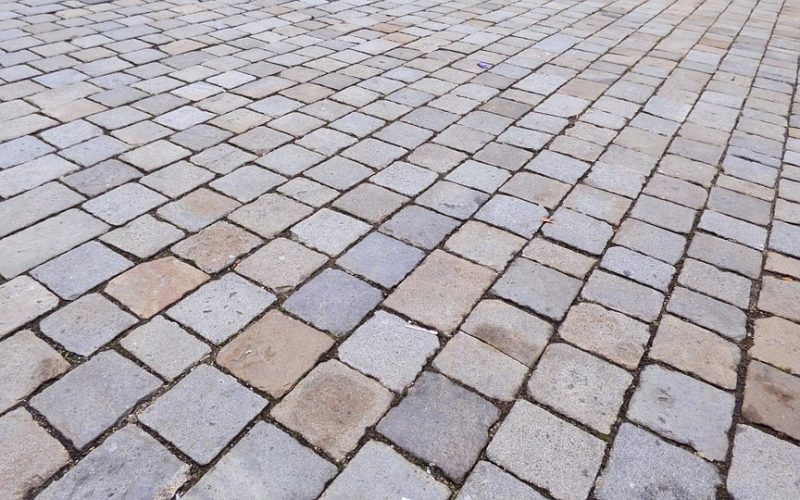
Stamped Concrete vs. Pavers: The Ultimate Homeowner’s Guide to Outdoor Surfaces
Choosing between stamped concrete and pavers for your outdoor living space is one of the most important decisions you’ll make during your home improvement journey. This comprehensive guide breaks down everything you need to know, from real-world costs to long-term performance, helping you make the smartest investment for your property.
Quick Comparison Chart: Stamped Concrete vs. Pavers
Factor | Stamped Concrete | Pavers & Slabs | Winner |
---|---|---|---|
Initial Cost | $8-$18 per sq ft | $10-$25 per sq ft | Stamped Concrete |
Installation Time | 2-3 days (500 sq ft) | 3-5 days (500 sq ft) | Stamped Concrete |
Lifespan | 20-30 years | 30-50+ years | Pavers |
Repair Difficulty | Complex (matching colors) | Simple (replace units) | Pavers |
Design Flexibility | High (patterns/textures) | Very High (modular) | Pavers |
Freeze-Thaw Performance | Good with proper sealing | Excellent | Pavers |
Maintenance Frequency | Every 2-3 years | Every 3-5 years | Pavers |
DIY Friendly | No | Moderate | Pavers |
Real-World Cost Analysis
Stamped Concrete Pricing Breakdown
- Basic Single Pattern: $8-$12 per square foot
- Materials: $3-$4/sq ft
- Labor: $4-$6/sq ft
- Sealing: $1-$2/sq ft
- Complex Multi-Pattern: $12-$18 per square foot
- Materials: $4-$6/sq ft
- Labor: $6-$10/sq ft
- Color hardener & release: $2/sq ft
- 500 sq ft Patio Example: $4,000 – $9,000 total
Paver Installation Pricing Breakdown
- Concrete Pavers: $10-$17 per square foot
- Materials: $3-$7/sq ft
- Base preparation: $2-$3/sq ft
- Labor: $5-$7/sq ft
- Natural Stone Pavers: $15-$25 per square foot
- Materials: $8-$15/sq ft
- Base & setting: $3-$4/sq ft
- Labor: $4-$6/sq ft
- 500 sq ft Patio Example: $5,000 – $12,500 total
Pro Tip: Don’t forget to factor in long-term costs. While stamped concrete is cheaper upfront, pavers often cost less over 20 years due to easier repairs and less frequent sealing requirements.
Stamped Concrete: The Complete Analysis
The Technology Behind Stamped Concrete
Modern stamped concrete has evolved significantly from its origins in the 1950s. Today’s installations use:
- Advanced Polymer-Modified Overlays: Providing better flexibility and crack resistance
- Integral Color Systems: UV-stable pigments mixed throughout the concrete
- Texture Mats: High-definition patterns that replicate natural materials with incredible accuracy
- Penetrating Sealers: Modern formulations that last 3-5 years instead of 1-2
Installation Process Explained
- Site Preparation (Day 1)
- Excavation to proper depth (4-6 inches)
- Compacted gravel base installation
- Form setup and reinforcement placement
- Concrete Pour (Day 2)
- 4,000 PSI concrete mix delivery
- Leveling and screeding
- Color hardener application
- Stamping Process (Day 2-3)
- Release agent application
- Pattern mat placement and stamping
- Detail work and touch-ups
- Finishing (Day 3-4)
- Pressure washing excess release
- Sealer application (2 coats)
- Curing time (24-48 hours)
Maintenance Schedule & Costs
Year | Maintenance Task | Cost (500 sq ft) |
---|---|---|
Annual | Cleaning & inspection | DIY: $20-30 |
Every 2-3 years | Resealing | $300-500 |
5-7 years | Minor crack repair | $200-400 |
10-15 years | Color restoration | $1,000-2,000 |
Common Problems & Solutions
- Surface Cracking:
- Cause: Improper curing, ground movement
- Solution: Crack filler and color matching ($100-300)
- Color Fading:
- Cause: UV exposure, poor quality sealer
- Solution: Tinted sealer application ($400-600)
- Delamination:
- Cause: Moisture issues, poor installation
- Solution: Overlay application ($6-8/sq ft)
Pavers & Slabs: The Complete Analysis
Types of Pavers Explained
Concrete Pavers
- Cost: $3-7 per sq ft (material)
- Strength: 8,000+ PSI
- Lifespan: 30-50 years
- Best for: Driveways, high-traffic areas
Natural Stone
- Cost: $8-15 per sq ft (material)
- Types: Granite, limestone, sandstone
- Lifespan: 50-100+ years
- Best for: Premium patios, pool decks
Clay Brick Pavers
- Cost: $5-10 per sq ft (material)
- Color: Permanent, kiln-fired
- Lifespan: 50+ years
- Best for: Traditional designs
Porcelain Pavers
- Cost: $8-12 per sq ft (material)
- Thickness: 3/4″ – 1.25″
- Features: Slip-resistant, stain-proof
- Best for: Modern designs, pool areas
Advanced Installation Techniques
The success of a paver installation lies in the base preparation:
- Excavation Depth Calculation:
- Pavers: 2.5-3 inches
- Sand bedding: 1 inch
- Base material: 4-6 inches (patios), 8-12 inches (driveways)
- Total excavation: 7.5-16 inches
- Base Materials by Application:
- Pedestrian areas: 3/4″ crushed stone
- Vehicular areas: Dense-graded aggregate
- Permeable installations: Open-graded aggregate
- Edge Restraint Options:
- Plastic restraints: $2-3 per linear foot
- Aluminum restraints: $4-6 per linear foot
- Concrete curbing: $8-12 per linear foot
Pattern Design Impact on Cost & Durability
Pattern | Labor Cost Impact | Structural Strength | Cut Waste % |
---|---|---|---|
Running Bond | Baseline | Good | 5-10% |
Herringbone 45° | +15-20% | Excellent | 10-15% |
Basketweave | +10% | Good | 5-8% |
Circular | +25-30% | Moderate | 15-20% |
Random | +20% | Very Good | 8-12% |
Climate & Regional Considerations
Performance by Climate Zone
Northern Climates (Freeze-Thaw Zones)
Stamped Concrete:
- Requires air-entrained concrete
- Annual sealing critical
- 25% higher crack risk
- Salt damage concerns
Pavers:
- Flexible joint system handles movement
- Individual unit replacement possible
- Better drainage reduces ice formation
- Salt-resistant options available
Winner: Pavers (significantly better performance)
Southern Climates (High Heat/UV)
Stamped Concrete:
- Light colors reflect heat better
- UV-stable sealers required
- Expansion joint spacing critical
- Surface can reach 140°F+
Pavers:
- Better heat dissipation through joints
- Light-colored options available
- Permeable pavers reduce heat island
- Surface typically 10-15°F cooler
Winner: Slight advantage to pavers
Soil Conditions Impact
- Clay Soils: Pavers perform better due to flexibility
- Sandy Soils: Both perform well with proper base
- Rocky Soils: Stamped concrete easier to install
- High Water Table: Permeable pavers offer drainage advantage
ROI & Property Value Impact
Resale Value Statistics
According to recent real estate studies and appraisal data:
- Stamped Concrete Patios:
- ROI: 50-70% of installation cost
- Property value increase: 2-3%
- Buyer perception: “Nice upgrade”
- Paver Installations:
- ROI: 70-85% of installation cost
- Property value increase: 3-5%
- Buyer perception: “Premium feature”
Total Cost of Ownership (20-Year Analysis)
Cost Factor | Stamped Concrete | Pavers |
---|---|---|
Initial Installation (500 sq ft) | $6,500 | $8,500 |
Sealing (every 2-3 years) | $3,000 | $1,000 |
Repairs & Maintenance | $2,500 | $1,500 |
Major Restoration (year 15) | $2,000 | $0 |
20-Year Total | $14,000 | $11,000 |
Your Decision Framework
Choose Stamped Concrete When:
- Budget is the primary concern
- You want a seamless, uniform appearance
- Project timeline is tight (need it done quickly)
- You’re in a mild climate with minimal freeze-thaw
- You’re comfortable with regular maintenance
- The area has minimal tree roots or soil movement
Choose Pavers When:
- Long-term value is more important than upfront cost
- You live in a freeze-thaw climate
- Easy repairs and low maintenance are priorities
- You may want to change the design later
- Drainage or permeability is important
- You’re planning to stay in the home 10+ years
Expert Recommendations by Use Case
Best Applications for Each Material
Driveways
Winner: Pavers
• Better load distribution
• Easier spot repairs
• No control joints
• Oil stain replacement possible
Pool Decks
Winner: Pavers
• Better slip resistance
• Cooler surface temperature
• No cracking from ground movement
• Chemical resistant options
Large Patios (1000+ sq ft)
Winner: Stamped Concrete
• Significant cost savings at scale
• Faster installation
• Seamless appearance
• Fewer joints to maintain
Walkways & Paths
Winner: Tie
• Both work well
• Pavers better for curves
• Stamped better for straight runs
• Consider matching existing materials
Professional Installation Tips
Contractor Selection Checklist:
- Minimum 5 years experience with your chosen material
- Local references you can visit/contact
- Proper licensing and insurance
- Detailed written warranty (2+ years)
- Portfolio showing similar projects
- Clear contract with material specifications
Hybrid Solutions to Consider
Don’t overlook these creative combinations that offer the best of both worlds:
- Stamped Concrete with Paver Borders: Cost-effective center with durable, repairable edges
- Paver Strips in Stamped Concrete: Creates expansion joints while adding design interest
- Mixed Material Zones: High-traffic areas in pavers, decorative areas in stamped concrete
Final Verdict: Making Your Decision
While both stamped concrete and pavers can create beautiful outdoor spaces, pavers edge out stamped concrete for most homeowners when considering the total lifecycle cost, durability, and flexibility. However, stamped concrete remains an excellent choice for budget-conscious homeowners in mild climates who prioritize immediate visual impact.
The 80/20 Rule: For 80% of homeowners, pavers will provide better long-term value despite the higher upfront cost. The remaining 20% who should strongly consider stamped concrete are those with large projects (1,000+ sq ft), tight budgets, or specific aesthetic requirements that pavers can’t match.
Next Steps
- Get Multiple Quotes: Prices vary significantly by region and contractor
- Visit Actual Installations: Photos don’t show texture and scale accurately
- Check References: Focus on installations 5+ years old to see real wear
- Consider Phasing: You can always start with one area and expand later
- Factor in Lifestyle: High entertainment use favors pavers’ durability
This guide represents current industry standards and pricing. Always verify local costs and building codes before starting your project.